
Engineering Experience
Sensata Technologies-Mechanical Engineer Intern
At Sensata, I designed and developed Temperature Response Validation System for AC Temperature sensor.
-
Developed temperature ramp system for high and low side fluid exchange to mimic an actual AC refrigeration cycle of a car.
-
Conducted calculations to select a centrifugal pump based on the required fluid flow rate.
-
Custom designed a thermal chamber for a car's under-hood environment simulation, thereby reducing costs by 80% and size by more than 90% making it portable.
-
Material selection to reduce thermal heat losses. Pushed heat losses to less than 2%.
-
Implemented autonomous actuation of fluid exchange 3-way valves using Arduino-based electronics.
-
Documented process control plans and BOM’s for future experimentation and implementation.
-
Collection of test data from Data Acquisition systems and analysis on Matlab.
Key Skills: Mechanical Design, Component and Material Selection, GD&T drawings, DFMA, Machine Design, CAD, Prototyping, Design of experiments, Fluid Mechanics, Steady-state Thermal Analysis, Material selection


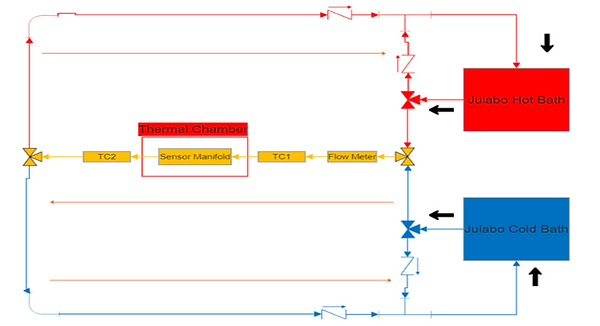




Indian Institute of Science-Mechanical Design and Research Intern
At IISc, India’s no. 1 research institution, I worked at the Surface Interaction and Manufacturing Lab under the guidance of Dr. Satish Vasu Kailash to research and devise low-cost, portable Tensile testing machine for micro-scale ductile materials, reducing cost by 35% compared to industrial standard. Implemented GD&T standard drawings for all the parts to be signed-off for manufacturing. Retrofitted capacitive plate sensor to measure displacement and load. Material selection and analysis based on various load boundary conditions.
Tensile Testing Machine specifications achieved
-
Linear movement: 1 micron/s to 3 mm/s.
-
Dual thread lead screw for specimen to move in opposite directions and weight reduction.
Key Skills: Mechanical Design, Structural analysis, Component and Material Selection, GD&T drawings, DFMA, Machine Design, CAD, Prototyping
Fraunhofer USA Center for Manufacturing Innovation - Automated Machine Development
Developed proof-of-concept Design of an Autonomous Micro-titer plate imaging machine for Fraunhofer USA Center for Manufacturing Innovation capable of imaging 4 plates of 96 wells each in a minute.
-
Conducted Torque, RPM and belt dimensions calculations to select motors and belts for actuation.
-
Sealed microtiter plates in a dark chamber for accurate imaging of contents in the wells.
-
Implemented autonomous loading and unloading of the microtiter plates from the stacks to save time and human resources and reduce costs.
-
Conducted pro-forma analysis to determine the feasibility of executing the machine and calculated NPV to be $957,216 with a payback period of 16 months.
-
Animation of the machine functionality.
Key Skills: Mechanical Design, Automated Machine Design, CAD, Material Selection, Component Selection, Pro-Forma and payback analysis, Brain storming, Concept Selection using Pugh charts
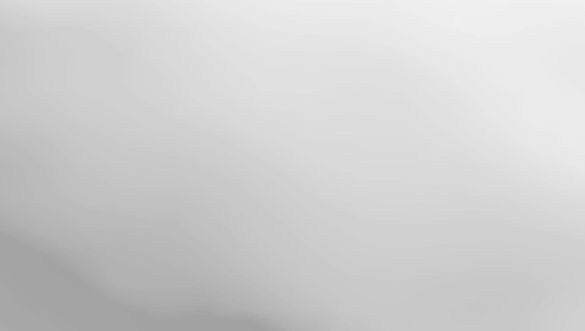
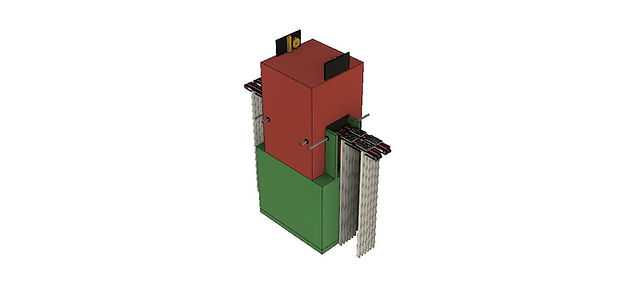




Boston University-VibroAid
Developing VibroAid, essentially a Band-aid that vibrates and helps heal wounds faster when specific frequency and amplitude values are spread across the wound.
-
Conducted Market Research to identify the problem and to learn about existing players in the industry.
-
Documented product requirements for the design and development of the product.
-
Programmed PCB to cause motor to vibrate on the wound site which is stacked upon a standard hydrocolloid gel pack to provide even vibrational frequency over entire wound site.
-
Product prototyping to achieve required functional requirements.
-
Placed electronics inside solidified bio-resin to reduce fabrication costs and to recycle electronics after usage.
-
Analyzed and prototyped adhesion of Bio-compatible resin over hydrocolloid gel pack. Conducted functional testing to verify the adhesion fit.
-
Built a custom-designed motor mount to constrain motor and mold design to pour resin over electronics.
-
Starting to venture as a startup in collaboration with BUild lab Boston University.
Key Skills: Prototyping, Mechanical Design, CAD, PCB electronics, Bio-Material Science, Medical Device Design, Business plan modelling. Cost analysis
Boston University-Design and Development of Rotary vane pump for drinking water
For the Design for Manufacturing and Production course capstone project, I designed and developed a rotary vane pump to pump drinking water under ambient room temperatures.
-
Analyzed the design for manufacturability and assembly for high-volume productions.
-
Conducted selection of manufacturing processes using aPriori to select most suitable and cost-effective manufacturing process for a part.
-
Material selection of pump parts by analyzing loading conditions and duty-cycle using Ansys Granta.
-
Produced GD&T engineering drawings for all the parts. Implemented drawings for the parts for different manufacturing processes such as casting, machining and injection molding and defining finish levels.
-
Conducted tolerance stack-up analysis of assembly and reduced interference between components.
-
Conducted draft analysis for parts that are casted or injection molded and tested its manufacturability.
-
Fabricated the entire model in machine shop using lathe, milling, laser cutting, waterjet cutting and sheet metal forming.
Key Skills: Mechanical Design, CAD, DFMA, Material selection using Ansys Granta, aPriori, GD&T drawings, Tolerance Stack-up analysis, draft analysis for casting and injection molding, Fabrication processes



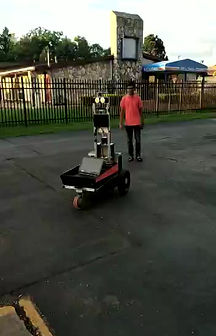
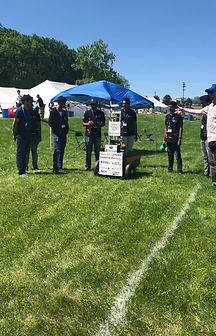

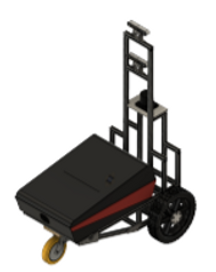

Designed and developed a fully autonomous ground vehicle that maneuvers an unknown path.
-
Developed an autonomous ground vehicle with Level 2 autonomy.
-
Designed accurate wheel and motor alignment of UGV and implementation of a castor wheel to accommodate a 360° rotation for the UGV.
-
Analyzed field of view of sensors by changing it to tadpole and delta alignment style and finalizing the better alignment.
Achievement: Won IGVC 2019 competition at Oakland University, Rochester, Michigan
Key Skills: Mechanical Design, CAD, DFMA, Material selection, Fabrication processes, Structural Analysis on Ansys Workbench
Link to Design report submitted to IGVC: http://www.igvc.org/design/2019/6.pdf
Boston University-Design and Manufacturing of Veggie Cutter
For the Product Realization course capstone project, we designed and manufactured a Veggie cutter with swappable cutting inserts
-
Developed a simple, reliable tool for cutting vegetables with interchangeable cutting frames.
-
Started with brainstorming of ideas and concept selection, finalized idea using Pugh charts.
-
Mechanical Design of the finalized concept.
-
Built a EVT prototype of all the components by 3D printing.
-
Developed an assembled DVT prototype with standard manufacturing processes.
-
Conducted various functional tests, quality test and drop tests to ensure product functionality.
-
Built and analyzed PVT prototype for mass production, DFMA, and packaging
-
Designed and Developed tooling plan for DVT and PVT stages of the product.
-
Developed process plan for manufacturing and assmebly.
-
Cost analysis of components using aPriori.
Key Skills: Prototyping, Mechanical Design, CAD, Business plan modelling. Cost analysis, EVT, DVT, PVT, Process plan documentation, BOM, Material Selection, Mold making, Draft analysis, Fabrication processes. DFMEA


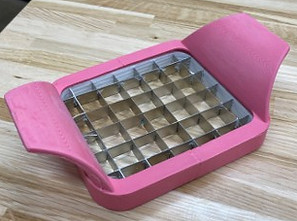






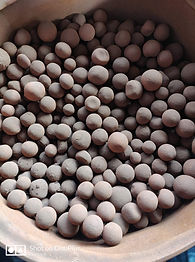
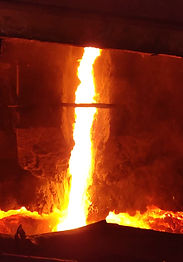


-
Interned at the world's 6th largest steel processing plant.
-
Gained working knowledge of iron and steel processing from Hematite(70%) and Magnetite(72% iron) ores.
-
Studied raw materials selection of iron ore, non-coking coal, coking coal, and limestone crudes for the production of high-grade steel.
-
Site visit to sinter and pellet plant to learn how iron ore is preprocessed before going into the Blast furnace. Sintering and Pelletization enhance the circulation of air in the blast furnace to aid smelting process.
-
Studied Iron and steel conversion by blast furnace and Corex technology.
-
Studied processing of iron and steel into cold rolled sheets of varying thickness, ingots, casted slabs and other byproducts.
-
Key Skills: Iron ore raw material handling, Iron and steel-making processes, Steel byproducts processing, Process documentation
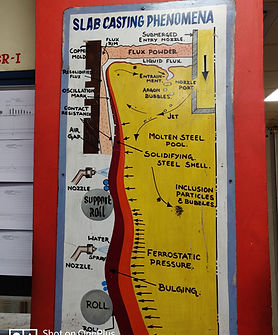


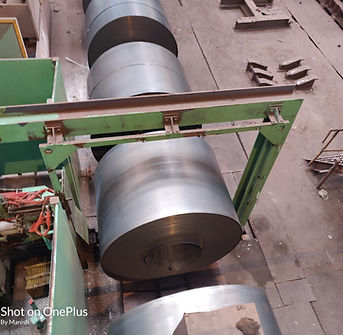
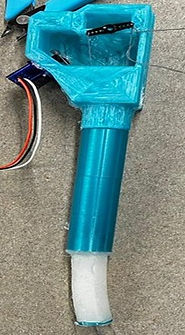
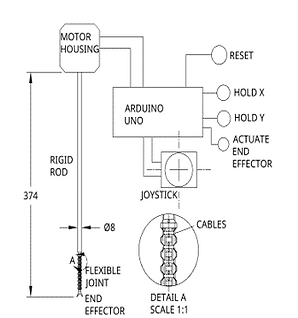
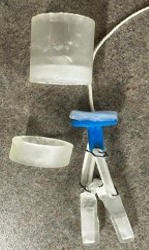

Boston University-Soft Actuated Laparoscope for grasping
For the Medical Robotics course capstone project, we designed and manufactured a Soft actuated laparoscope.
-
Mechanical Design of soft actuator and a grasping end effector and iterating design to obtain functional laparoscopic tool.
-
Fabricated soft actuator by a flexible 3D printed material and controlled by motors, and joysticks with a programmed Arduino.
-
Implemented a cable driven actuation system to maneuver the soft actuator and end effector to reduce dexterity and mitigate fulcrum effect.
-
Calculated pulley dimensions, motor torque required and selected components.
-
Evaluated performance of this device with a traditional laparoscope utlizing NASA task loader.
-
Incorporated a single-piece mechanism that combines lateral and transverse axis control.
Key skills: Prototyping, Mechanical Design, CAD, PCB electronics, Bio-Material Science, Medical Device Design, Business plan modelling. Cost analysis, 3D printing
To develop an autonomous aerial vehicle that can perform the essential flight functions, i.e., roll pitch and yaw autonomously along with payload delivery.
-
Implemented Mechanical Design on Fusion 360 for maintaining thrust to weight ratio and fuselage to arm ratio for stability and maneuverability.
-
Performed various analysis on Ansys Workbench to optimize design such as CFDs, Static Structural, and Design for Manufacturing and Assembly (DFMA).
Key Skills: Mechanical Design, CAD, DFMA, Material selection, GD&T drawings, Fabrication processes, Structural and CFD Analysis on Ansys Workbench, Prototyping, 3D printing
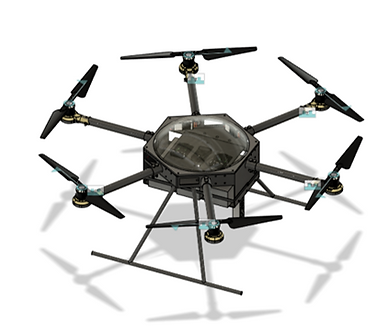


HPVC( Human Powered Vehicle Competition)
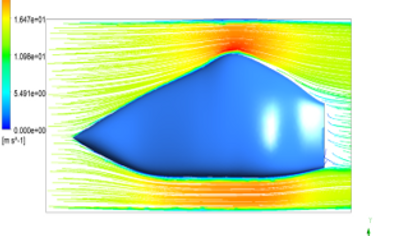
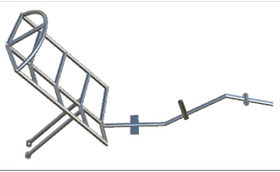

Participated in the ASME E Fest HPVC in 2020.
-
Designed and analyzed different structures for HPV, i.e. Delta trike and Tadpole trike through simulations.
-
Iterated 3 designs and finalized concepts using Pugh charts and simulations.
-
Designed chassis frame based on concept selection and optimized using structural simulations.
-
Designed welding joints and selection of welding process for fabrication.
-
Hands-on fabrication of the chassis- frame.
-
Analyzed design of closed loop, roll hoop, and fairing integrated systems Roll-over protection systems.
-
Performed CFD analysis for fairing to analyze and reduce drag forces.
-
Performed different bike inspection levels, such as load, endurance, and speed tests.
Key Skills: Mechanical Design, CAD, DFMA, Material selection, CFD, Fabrication processes, Structural Analysis on Ansys Workbench, Concept Selection using Pugh charts
College of Aviation Technology- Aircraft Design Intern
-
Designed commercial aircraft structural body with minimal drag coefficient by design iterations.
-
Iterated design to ensure a low C.G. placing wings at bottom half of fuselage and nearer to root of the wing.
-
Tested designs using wind tunnel simulations and selected best structure.
-
Published as Research Paper titled “Development of Next Generation Civilian Aircraft” in the “IJSER Journal” December 2020 edition.
Key Skills: Mechanical Design, CAD, DFMA, Material selection, Structural and CFD Analysis on Ansys Workbench, Aircraft Design







Mahindra Rise Prize Driverless Challenge
Innovation challenge to develop Mahindra E20 car to an Autonomous vehicle capable of driving on Indian road conditions.
-
Developed a Mahindra E20 car into an Autonomous vehicle capable of driving on Indian road conditions.
-
Implemented Drive by Wire system to make Mahindra Electric Car fully actuator-based control.
-
Precisely designed and manufactured mounts for different sensors deployed for autonomy, such as 3D Lidar, 2D Lidar, Ultrasonic sensors, Ximea Speed Cams, and Radars.
Achievement: One of the finalists of the Mahindra Spark the Rise challenge.
Key Skills: Mechanical Design, CAD, Material selection, Fabrication processes, 3D printing, Drive by Wire
ASME- IAM3D (Innovative Additive Manufacturing) Competition
Innovative Additive Manufacturing 3D challenges you to develop solutions to problem statements utilizing the full potential of 3D printing.
-
Designed, analyzed for possible design changes employing CFD and Structural simulations and iterations helping the drone to be structurally stable and reducing the drag coefficient.
Key Skills: Mechanical Design, CAD, DFMA, Material selection, Fabrication processes, Structural and CFD Analysis on Ansys Workbench, Prototyping, 3D printing



This competition from India's premier institute is aimed at testing student teams' capability to build a remote-controlled bot to place a cube of specific dimensions in strategic positions to make a pathway for it to traverse and avoid obstacles in its course.
-
Designed and analyzed 4 bar linkage mechanisms to hold the objects by utilizing gearing mechanism and pneumatics.
-
Bolstered kinematics, dynamics, control theory, electronics, skills, and application of Mechanical engineering concepts.
Key Skills: Mechanical Design, CAD, Material selection, Fabrication processes, Structural Analysis on Ansys Workbench
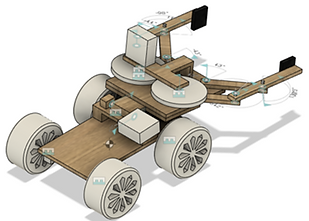



Covid 19 Hackathon
-
Developed an efficient intubation box to help doctors and nurses to operate on Covid infected patients with minimal contact.
-
Communicated with students of KMC Hospital, Manipal, and gained knowledge of the requirements of the intubation box design with all the necessary attributes.
-
Designed the intubation box with unique features such as replaceable hand gloves attachment at the entry of the doctors’ hand to ensure sterilization of used gloves.
Key Skills: Mechanical Design, Component and Material Selection, CAD, Medical Equipment Design

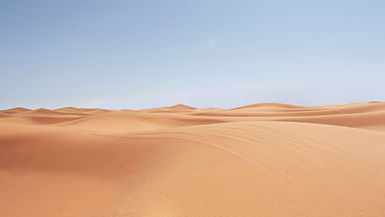